Industrial Automation Systems: Unleashing the Power of Industrial Automation Systems
Welcome to the future! From assembly lines to warehouses, industrial automation systems are revolutionizing the way we work and produce. These intelligent machines have become the backbone of countless industries, maximizing efficiency, accuracy, and productivity like never before. In this blog post, we will dive deep into the fascinating world of industrial automation systems and explore how they are unleashing their immense power to reshape our present and shape our tomorrow. So fasten your seatbelts and get ready for an exciting journey into a realm where human ingenuity meets cutting-edge technology – welcome to the era of Industrial Automation Systems: Unleashing the Power!
What is Industrial Automation Systems?
Industrial Automation Systems (IAS) are computer-based systems used to control and optimize industrial production processes. IAS can be used in a variety of industries, including manufacturing, mining, oil and gas, power generation, and food and beverage processing.
IAS can improve productivity, quality, safety, and sustainability in industrial settings. They can also help to reduce costs by automating tasks that would otherwise need to be performed manually. In some cases, IAS can even be used to monitor and control processes remotely.
There are many different types of IAS available on the market today. Some common examples include programmable logic controllers (PLC), supervisory control and data acquisition (SCADA) systems, and distributed control systems (DCS).
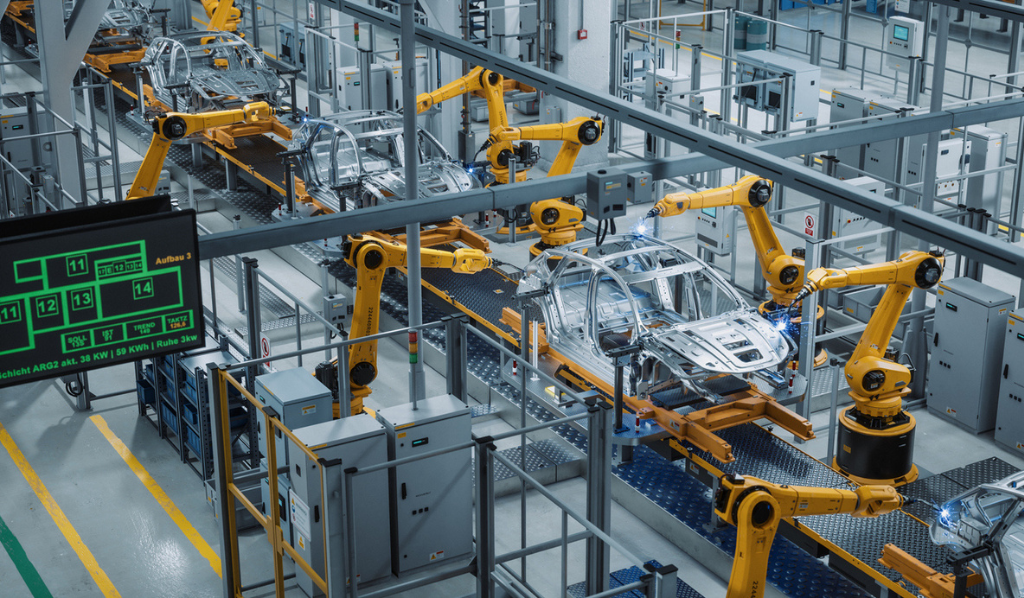
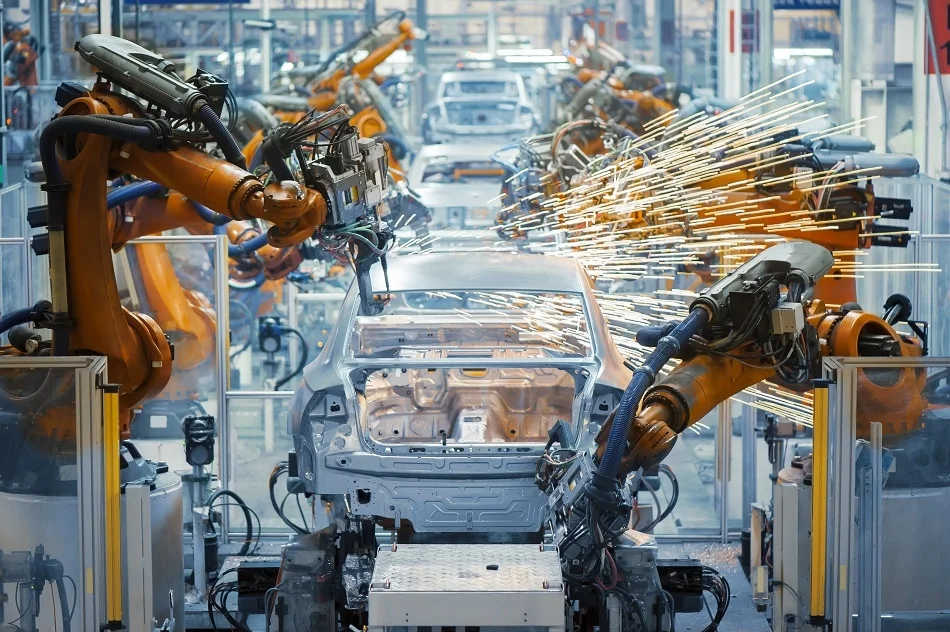
Benefits of Industrial Automation Systems
Industrial automation systems have revolutionized the manufacturing process by providing a means to increase production while reducing costs. By automating repetitive and time-consuming tasks, these systems have freed up workers to focus on more value-added activities, such as product development and customer service.
In addition to increased efficiency, industrial automation systems offer a number of other benefits, including:
- Improved quality control: Automated systems can monitor production processes and identify errors or potential problems more quickly than human workers. This helps to ensure that products meet quality standards and reduces the need for costly repairs or replacements.
- Greater flexibility: Automated systems can be easily reconfigured to accommodate changes in product design or customer demand. This allows manufacturers to respond quickly to market changes and keep up with the competition.
- Reduced downtime: Automated systems are less likely to break down than traditional machinery, meaning that production can be maintained at a higher level for longer periods of time. This minimizes disruptions and keeps costs low.
Types of Industrial Automation Systems
There are three types of industrial automation systems: continuous, batch, and discrete.
Continuous automation systems are used when products need to be produced at a constant rate without interruption. These systems typically use an assembly line where each workstation performs a specific task and products move from one station to the next.
Batch automation systems are used when products need to be produced in batches rather than continuously. These systems typically have several workstations that can produce different products or perform different tasks. Products are usually made in groups or batches and then moved to the next station for further processing.
Discrete automation systems are used when products need to be produced individually rather than in batches. These systems typically have several workstations that can produce different products or perform different tasks. Each product is made individually and then moved to the next station for further processing.
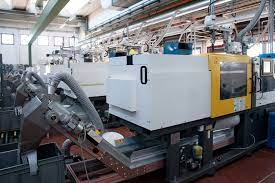
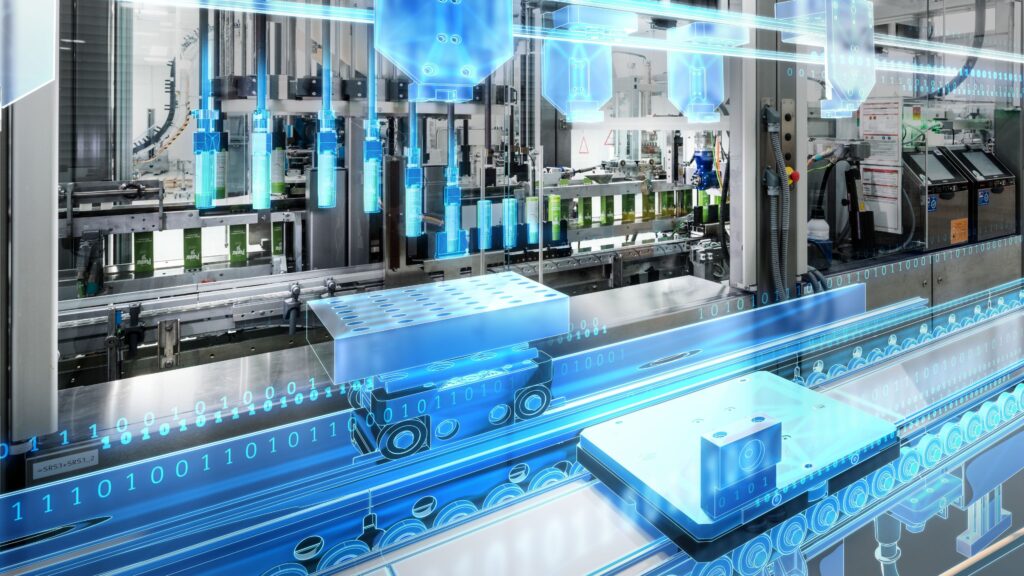
How to Implement Industrial Automation Systems?
Industrial automation systems are the key to unlocking the power of industrial automation. By automating processes and tasks, these systems can help you improve productivity, efficiency, and quality while reducing costs. But how do you go about implementing an industrial automation system?
Here are some tips:
- Define your goals and objectives. What do you hope to achieve with industrial automation? Improved productivity? Increased efficiency? Higher quality? Reduced costs? All of the above? Be specific.
- Assess your current state. Where are you starting from? Do you have existing automated processes in place that can be expanded upon? Are you starting from scratch? Knowing your starting point will help you create a roadmap for implementation.
- Choose the right technology. There are many different types of industrial automation technologies available, so it’s important to choose the one that best fits your needs. Consider factors such as cost, complexity, compatibility with existing systems, and scalability when making your decision.
- Develop a plan. Once you’ve chosen the right technology, it’s time to develop a plan for implementation. This should include a timeline, budget, and resources needed. Make sure to involve all stakeholders in the planning process so everyone is on the same page.
- Implement and test. Follow your plan to implement the new system, being sure to test along the way to ensure everything is working as intended. Once everything is up and running, monitor
Challenges in Implementing and Managing Industrial Automation Systems
The challenges in implementing and managing industrial automation systems can be many and varied. They can include everything from the technical challenges associated with integrating the various components of the system, to the logistical challenges of managing and coordinating the activities of all the different stakeholders involved in the project.
One of the most significant challenges is often simply getting everyone on board with the project. In many cases, industrial automation systems are seen as a threat to jobs, and so there can be a lot of resistance from employees. It is therefore essential to have a clear and compelling case for why the system is being introduced, and how it will benefit both the company and its employees.
Another challenge is ensuring that the system is designed in such a way that it meets all the required regulatory standards. This can be a complex process, as there may be multiple stakeholders involved who all have their own agendas. It is therefore important to have a clear understanding of all the relevant standards before starting work on the design of the system.
Once the system is up and running, there is always the challenge of maintaining it and keeping it up-to-date. This can be a difficult task, as technology evolves rapidly and new versions of software and hardware are constantly being released. It is therefore important to have a good support infrastructure in place so that any issues can be quickly resolved.
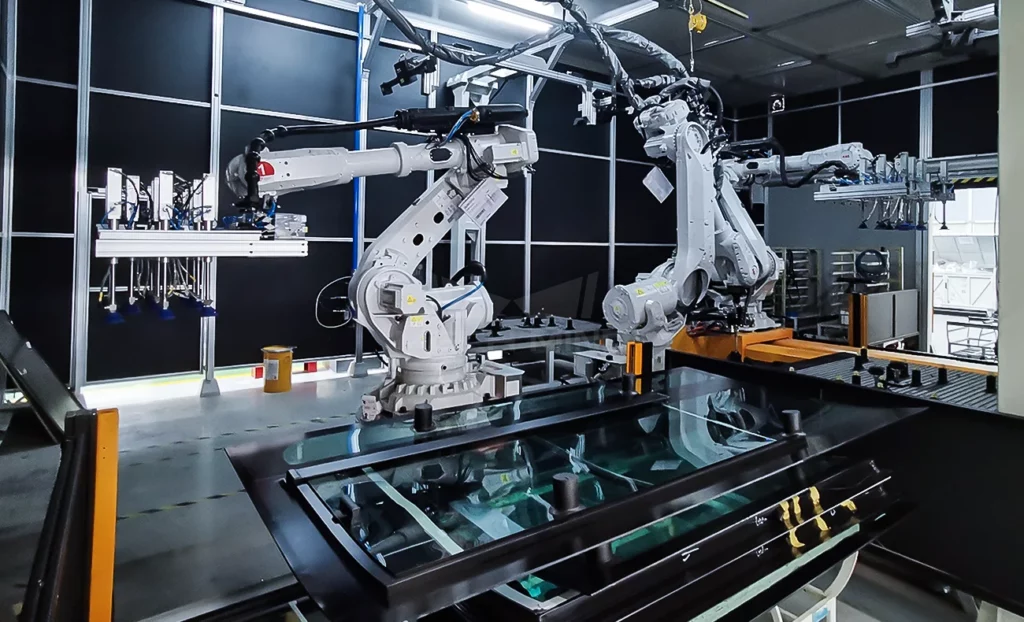
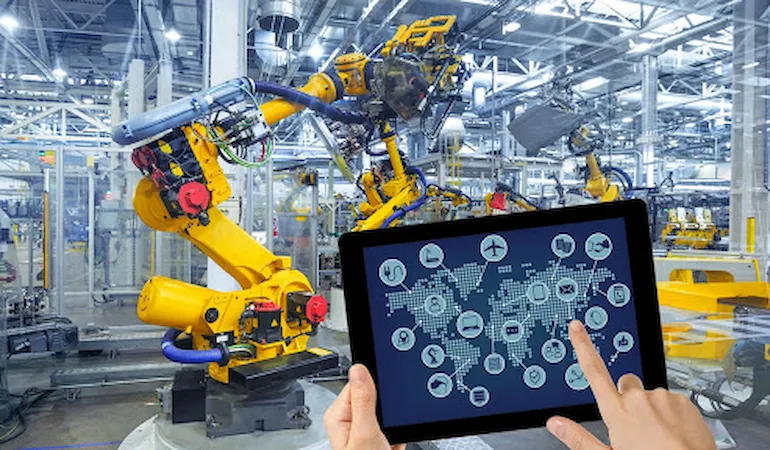
Examples of Industrial Automation Systems
- Programmable logic controllers (PLCs) are perhaps the most commonly used type of industrial automation system. PLCs are small, modular units that can be programmed to control a variety of different processes.
- Human-machine interfaces (HMIs) are another common type of industrial automation system. HMIs provide a graphical interface that allows operators to interact with and monitor the status of various machines and processes.
- Distributed control systems (DCSs) are more complex than PLCs or HMIs, but they offer significant advantages in terms of flexibility and expandability. DCSs typically consist of multiple controllers that are networked together and can be used to manage large, distributed systems.
- Supervisory control and data acquisition (SCADA) systems are used in a variety of industries to monitor and control large-scale processes. SCADA systems typically include both hardware and software components, and they can be used to monitor everything from factory floors to power grids.
Conclusion
Industrial automation systems represent the future of industrial production. By leveraging artificial intelligence, machine learning, and robotics technology, these systems can enable businesses to increase their productivity and improve quality while reducing costs. With the right implementation strategy in place, companies can unlock tremendous value from industrial automation systems and position themselves for success in a rapidly changing market.
Our Products
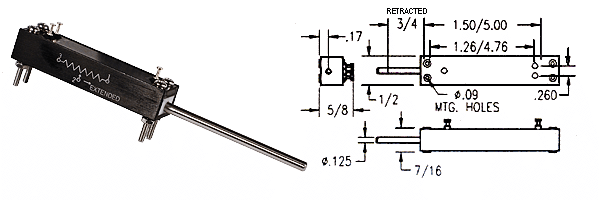
Conductive Plastic Element Black Anodized Aluminum Body, Stainless Steel Shaft, Gold Plated Terminals Recommended for Test and Lab Equipment, Industrial Applications, Medical Equipment (non-life support) Life Expectancy: 20 million strokes Resistance Tolerance: 20% standard (10% Available) Linearity Tolerance: .5% to 1.5% standard (0.3% to 1.0% Available) Power Rating: 0.2 to 1.2 Watt Electrical Stroke: 1″ […]
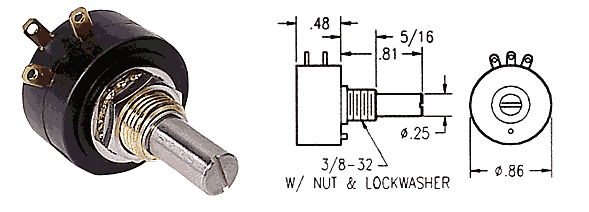
Conductive Plastic Element. Gold Plated Terminals. High Temp. Thermoplastic Housing. Stainless Steel Shaft. Recommended for Medical Equipment (non-life support), Robotics, Industrial, Test and Lab Equipment. Life Expectancy: 10 million turns Resistance Tolerance: ± 10% standard ( ± 10% available) Linearity Tolerance: ± 1.0% standard ( ± 0.5% available) Electrical Angle: 320º ± 5º Mechanical Angle: […]
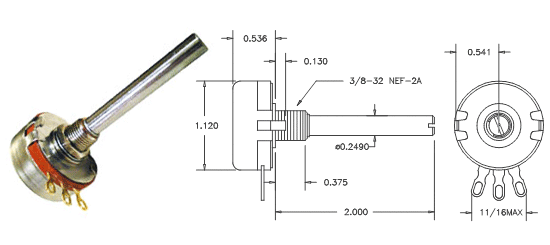
Hot molded carbon element Gold-plated terminals Stainless-steel shaft and housing Quality meeting or exceeding MIL-R-94 – QPL listed Rotational Life: 25,000 Resistance Tolerance: ± 10% or ± 20% Operating Temperature Range: -65°C to +125°C Power rating: 2 watts Insulation Resistance – dry: 10K Meg; wet: 100K Meg Dielectric Strength: 900 VRMS Starting Torque: 1 oz/in […]
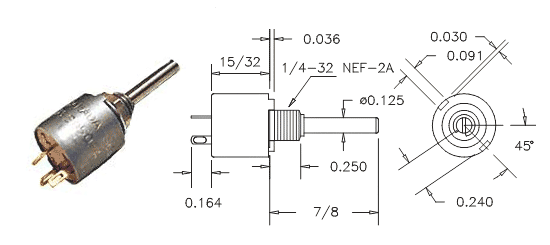
Hot molded carbon element One piece housing and bushing Stainless-steel shaft Quality meeting or exceeding MIL-R-94 – QPL listed Rotational Life: 25,000 Resistance Tolerance: ± 10% or ± 20% Operating Temperature Range: -65°C to +125°C Power rating: 0.5 watts Insulation Resistance – dry: 10K Meg; wet: 100K Meg Dielectric Strength: 750 VRMS Operating Torque: 0.5 […]
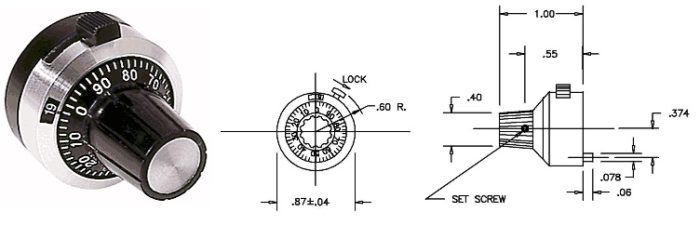
MG22 Concentric Turns Counting Dial Counts up to 20 turns. One Piece Mounting. Aluminum Housing. Black Nylon Knob. Numbers are White on Black Background. Over the Center Lock Available. Diameter – 7/8″; Extension from Panel – 1.0″ Maximum Panel Thickness – 1/4″ Weight: .2 oz
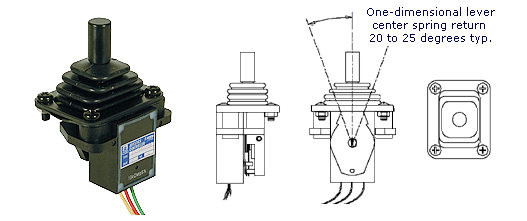
Electrical Specifications: 10K ohm precision potentiometer Single axis joystick Cylindrical knob Linearity (independent): ± 5.0% Lever Electrical Angle: 40° Max. Resolution: Essentially Infinite Mechanical Specifications: ± 20° from center deflection angle Life expectancy: 5 million operations Spring return to center Housing material: High temp. thermoplastic IP65 Rating
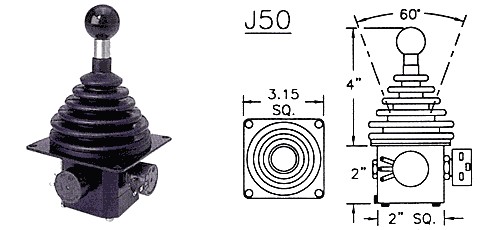
Two axis joystick 4″ handle height 60° deflection angle ( ± 30°) Ball knob Spring return to center Circular deflection pattern 10K ohm precision potentiometer Protective rubber boot (IP54 rating above panel) IP65 option available upon special request Panel mounting bracket
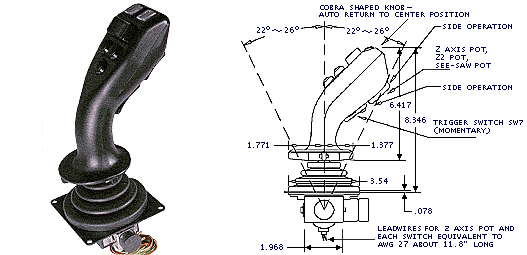
Multi-axis joystick 8.34″ handle height 45° deflection angle ( ± 22.5°) Spring return to center Cobra Head handle Circular deflection pattern 10K ohm precision potentiometers – all axis Three momentary switches (two illuminated, one trigger) Panel mounting bracket Protective rubber boot (IP65 rating above panel)
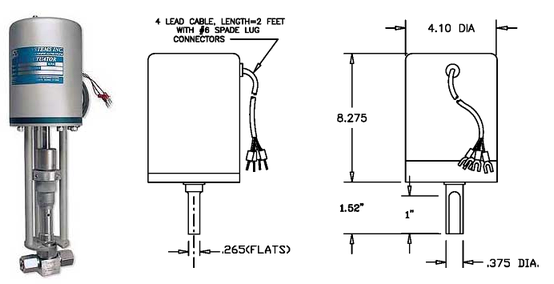
Input: 4 to 20 mA (200 ohms) or 0 to 10VDC (18KΩ) Rotation Speed : 1.5, 3, 5, 10, 20 or 40 RPM Power : 24 VDC (50 Watts min.) Dynamic Braking : Installed Limit Switches : Installed Torque Limiter : Set for Valve requirements. Wt : Approx. 21 in/lbs. max. Seating Limiter : Set […]
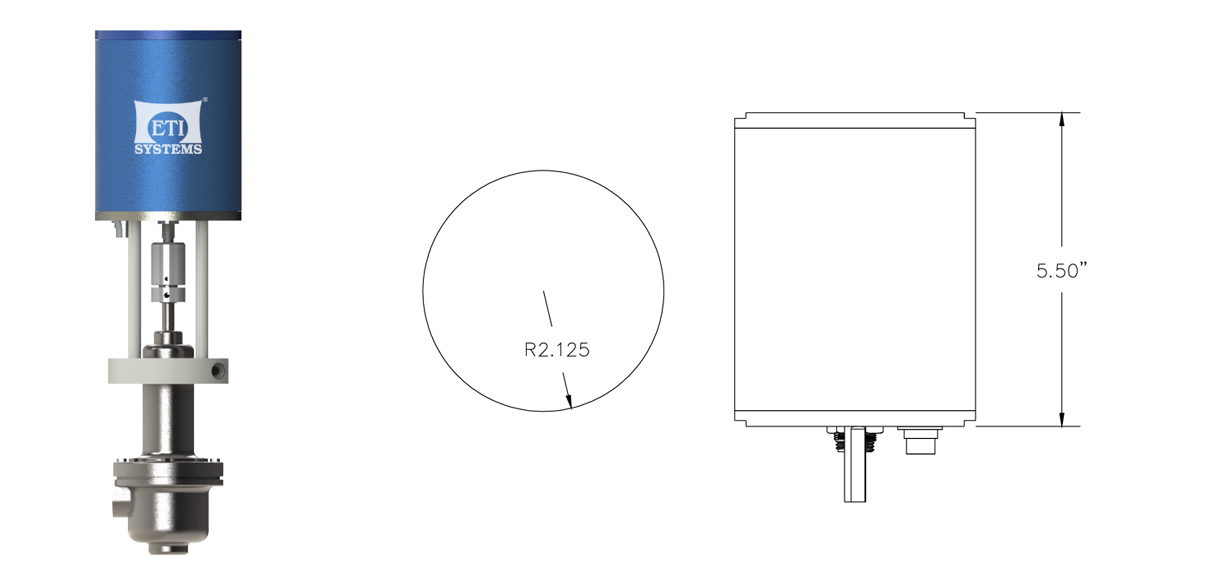