Electric Valve Actuators: Embracing Electric Valve Actuators for Optimal Performance
Are you tired of dealing with manual valve actuators that require constant maintenance and can be a hassle to operate? It’s time to embrace the future of valve automation – electric valve actuators! With their unparalleled performance, efficiency, and ease of use, these cutting-edge devices are revolutionizing industries worldwide. In this blog post, we’ll dive into the world of electric valve actuators and explore how they can optimize your operations for maximum productivity. Get ready to say goodbye to outdated technology and hello to a new era of seamless automation!
Introduction to Electric Valve Actuators
Electric valve actuators are devices that use electric signals to control the opening and closing of valves. They are used in a variety of industries, including oil and gas, water treatment, and HVAC. Electric valve actuators offer several advantages over manual or pneumatic actuators, including more precise control, higher reliability, and lower maintenance costs.
When selecting an electric valve actuator, it is important to consider the application and required torque. Other factors such as voltage, power consumption, enclosure type, and certifications may also be important.
Types of Electric Valve Actuators
There are two main types of electric valve actuators: direct-acting and reverse-acting. Direct-acting actuators open the valve when energized and close it when de-energized. Reverse-acting actuators do the opposite: they close the valve when energized and open it when de-energized.
The most common type of direct-acting actuator is the solenoid actuated ball valve. This type of actuator uses a magnetic field to move a plunger that opens or closes the valve. Solenoid actuated ball valves are often used in applications where fast response times are required, such as in irrigation systems.
Reverse-acting actuators are more commonly used than direct-acting ones because they have certain advantages, such as being fail-safe (i.e., the valve will close if there is a
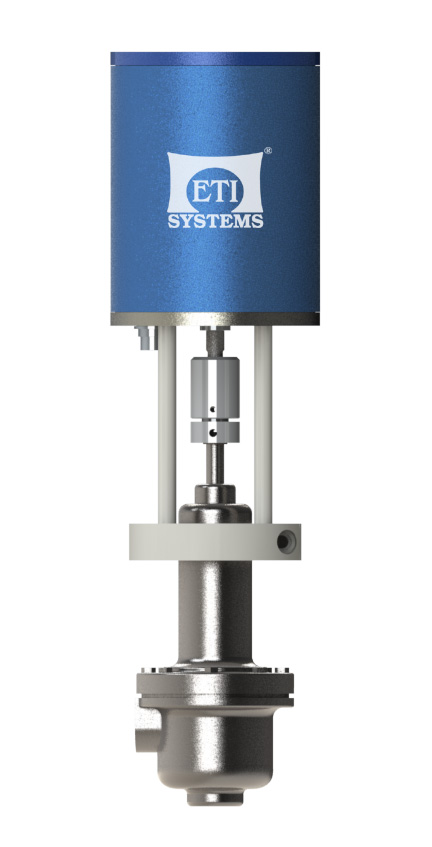
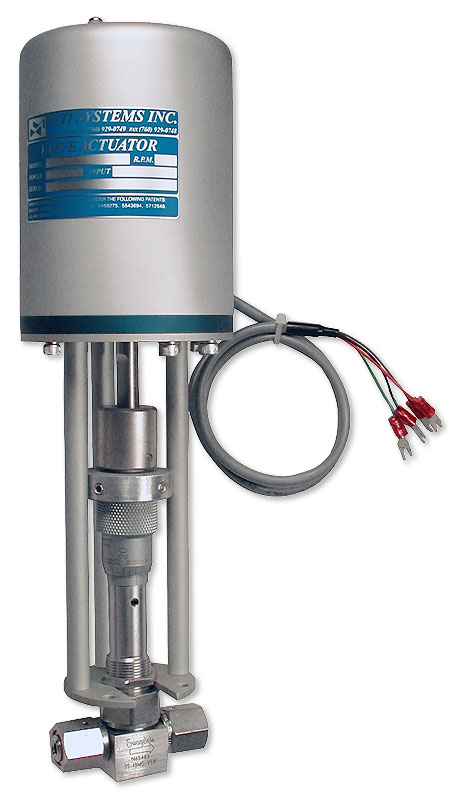
Advantages of Electric Valve Actuators
Electric valve actuators offer many advantages over manual or pneumatic actuators. Here are just a few reasons why you should consider electric valve actuators for your next project:
- Electric valve actuators are more precise than manual or pneumatic actuators. This means that you can control the flow of fluid more precisely, which can improve process control and efficiency.
- Electric valve actuators are easier to operate than manual or pneumatic actuators. This is because they don’t require as much force to operate, so they can be operated with less effort.
- Electric valve actuators have a longer lifespan than manual or pneumatic actuators. This is due to the fact that they don’t have any moving parts that can wear out over time.
- Electric valve actuators are more energy efficient than manual or pneumatic actuators. This is because they use less power to operate, which can save you money on your energy bills.
Types of Electric Valve Actuators
Electric valve actuators are devices that use electrical energy to open or close a valve. There are many different types of electric valve actuators, each with its own advantages and disadvantages. The most common type of electric valve actuator is the solenoid-type actuator. Solenoid-type actuators are simple, reliable, and relatively inexpensive. However, they are not well suited for high-pressure or high-temperature applications. Another type of electric valve actuator is the pneumatic-type actuator. Pneumatic-type actuators use compressed air to open or close a valve. Pneumatic-type actuators are more expensive than solenoid-type actuators, but they can be used in high-pressure and high-temperature applications.
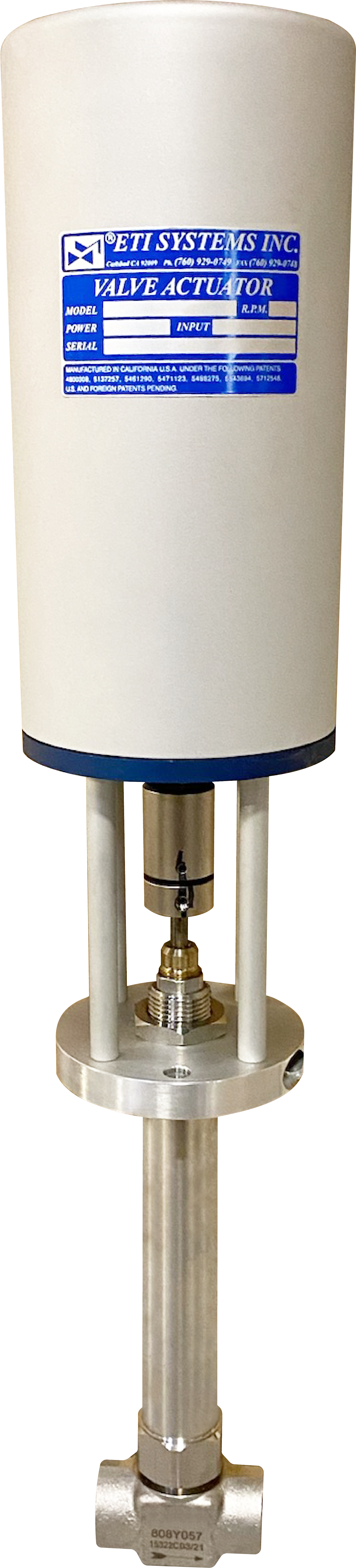
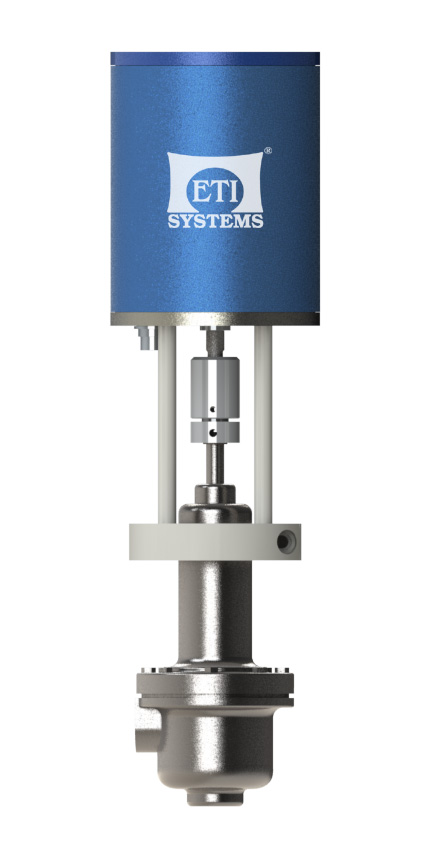
How to Select the Right Electric Valve Actuator
When it comes to electric valve actuators, there are many factors to consider in order to select the right one for your needs. Here are a few key considerations:
- Torque requirements: One of the most important considerations when choosing an electric valve actuator is the required torque. This will determine the size and type of actuator you need.
- Voltage and power requirements: Another key consideration is the voltage and power requirements of the actuator. This will ensure that you choose an actuator that can handle the power needed for your application.
- Environmental conditions: You’ll also need to consider the environmental conditions in which the actuator will be used. This includes temperature, humidity, and other factors that could affect performance.
- Certification: When selecting an electric valve actuator, it’s important to make sure that it is certified for use in your particular application. This will give you peace of mind knowing that the actuator meets all safety standards.
Maintenance and Troubleshooting of Electric Valve Actuators
Electric valve actuators are devices that use electrical energy to move or control valves. They are often used in lieu of manual actuators, which require manual operation. Electric valve actuators can be used in a variety of industries, including oil and gas, water and wastewater, chemical processing, and food and beverage processing.
When selecting an electric valve actuator, it is important to consider the required torque, operating environment, power requirements, and certifications. Additionally, proper installation and regular maintenance are critical for optimal performance. This section will provide an overview of electric valve actuator maintenance and troubleshooting.
To prevent problems before they start, it is important to follow the manufacturer’s recommended maintenance schedule for your particular model of electric valve actuator. Maintenance tasks may include lubricating moving parts, checking wiring and connections, and inspecting the unit for signs of wear or damage. If any problems are found during routine maintenance, they should be addressed immediately to avoid further damage or downtime.
If an electric valve actuator stops working properly, there are a few potential causes that should be considered. First, check the power supply to ensure that the unit is receiving electricity. Next, check for loose wires or other electrical problems. If the unit is still not functioning properly, it may need to be replaced or repaired by a qualified technician
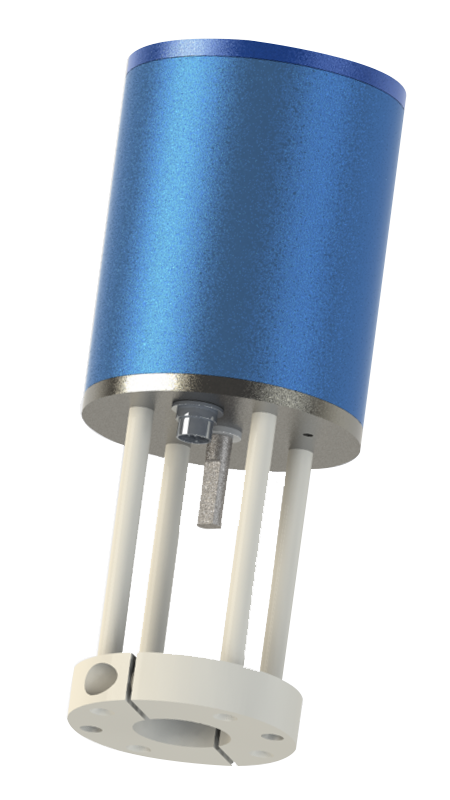
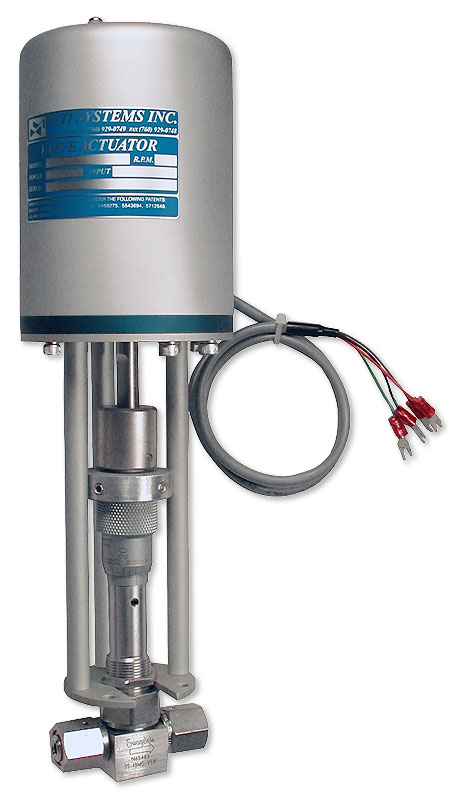
Application Examples of Electric Valve Actuators
Electric valve actuators are used in a variety of industries and applications. Here are a few examples:
In the food and beverage industry, electric valve actuators are used to control the flow of liquids and gases. For example, they can be used to open and close valves that regulate the flow of beer through a brewing system.
In the oil and gas industry, electric valve actuators are used to control the flow of oil and gas. For example, they can be used to open and close valves that regulate the flow of oil through a pipeline.
In the chemicals industry, electric valve actuators are used to control the flow of chemicals. For example, they can be used to open and close valves that regulate the flow of chlorine through a water treatment plant.
Alternatives to Electric Valve Actuators
There are a few alternatives to electric valve actuators, each with their own set of pros and cons. The most common alternatives are pneumatic and hydraulic actuators.
Pneumatic actuators use compressed air to power the movement of the valve. They are often used in applications where electric power is not available or where explosion-proofing is required. Pneumatic actuators can be powered by a variety of energy sources, including solar power. However, they require regular maintenance and can be difficult to control accurately.
Hydraulic actuators use fluid pressure to power the movement of the valve. They are often used in high-pressure applications or where precise control is required. Hydraulic actuators can be powered by a variety of energy sources, including solar power. However, they require regular maintenance and can be difficult to control accurately.
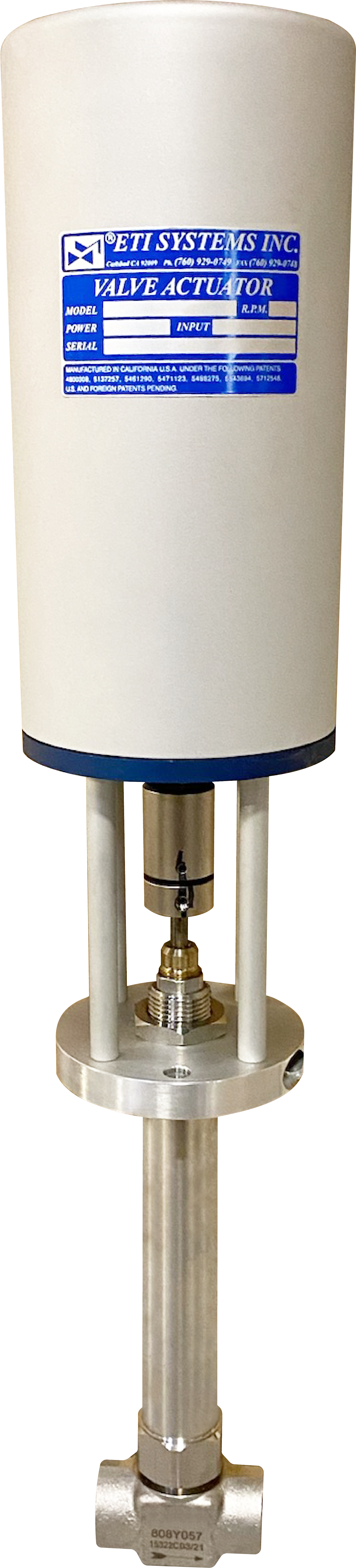
Conclusion
In conclusion, electric valve actuators have been proven to be a reliable and cost-effective option for controlling fluid flow in a variety of applications. They offer significant advantages over other types of manual or pneumatic actuators in terms of speed, accuracy, reliability and cost savings. For these reasons, electric valve actuators are becoming increasingly popular in many industrial settings and it is important for professionals to understand the latest technology available so that they can make the best possible decisions for their particular application needs.
Our Products
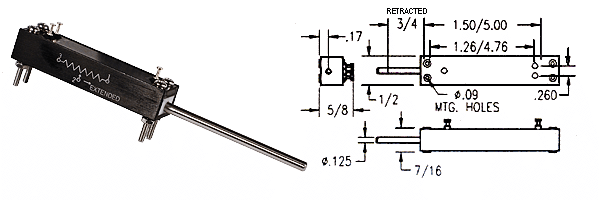
Conductive Plastic Element Black Anodized Aluminum Body, Stainless Steel Shaft, Gold Plated Terminals Recommended for Test and Lab Equipment, Industrial Applications, Medical Equipment (non-life support) Life Expectancy: 20 million strokes Resistance Tolerance: 20% standard (10% Available) Linearity Tolerance: .5% to 1.5% standard (0.3% to 1.0% Available) Power Rating: 0.2 to 1.2 Watt Electrical Stroke: 1″ […]
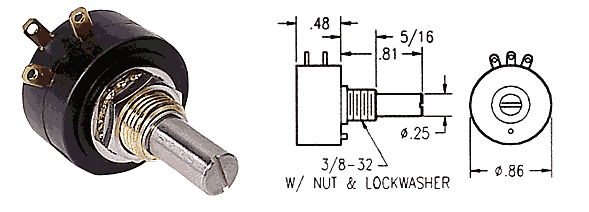
Conductive Plastic Element. Gold Plated Terminals. High Temp. Thermoplastic Housing. Stainless Steel Shaft. Recommended for Medical Equipment (non-life support), Robotics, Industrial, Test and Lab Equipment. Life Expectancy: 10 million turns Resistance Tolerance: ± 10% standard ( ± 10% available) Linearity Tolerance: ± 1.0% standard ( ± 0.5% available) Electrical Angle: 320º ± 5º Mechanical Angle: […]
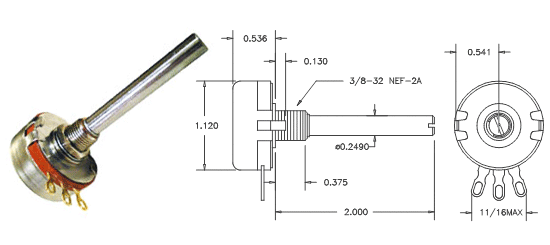
Hot molded carbon element Gold-plated terminals Stainless-steel shaft and housing Quality meeting or exceeding MIL-R-94 – QPL listed Rotational Life: 25,000 Resistance Tolerance: ± 10% or ± 20% Operating Temperature Range: -65°C to +125°C Power rating: 2 watts Insulation Resistance – dry: 10K Meg; wet: 100K Meg Dielectric Strength: 900 VRMS Starting Torque: 1 oz/in […]
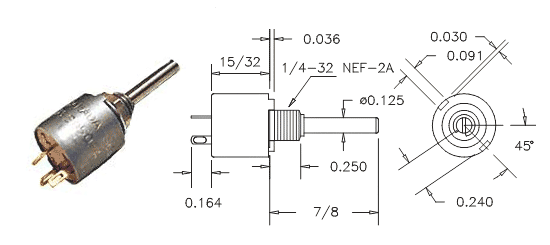
Hot molded carbon element One piece housing and bushing Stainless-steel shaft Quality meeting or exceeding MIL-R-94 – QPL listed Rotational Life: 25,000 Resistance Tolerance: ± 10% or ± 20% Operating Temperature Range: -65°C to +125°C Power rating: 0.5 watts Insulation Resistance – dry: 10K Meg; wet: 100K Meg Dielectric Strength: 750 VRMS Operating Torque: 0.5 […]
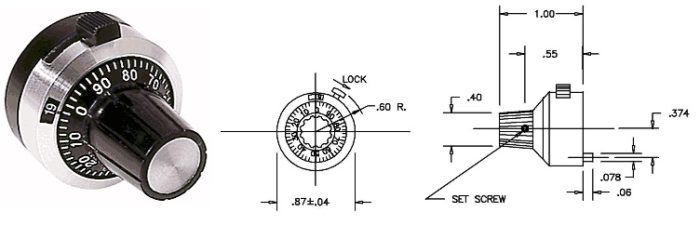
MG22 Concentric Turns Counting Dial Counts up to 20 turns. One Piece Mounting. Aluminum Housing. Black Nylon Knob. Numbers are White on Black Background. Over the Center Lock Available. Diameter – 7/8″; Extension from Panel – 1.0″ Maximum Panel Thickness – 1/4″ Weight: .2 oz
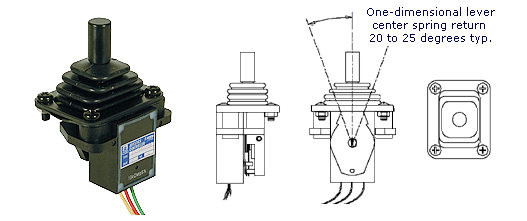
Electrical Specifications: 10K ohm precision potentiometer Single axis joystick Cylindrical knob Linearity (independent): ± 5.0% Lever Electrical Angle: 40° Max. Resolution: Essentially Infinite Mechanical Specifications: ± 20° from center deflection angle Life expectancy: 5 million operations Spring return to center Housing material: High temp. thermoplastic IP65 Rating
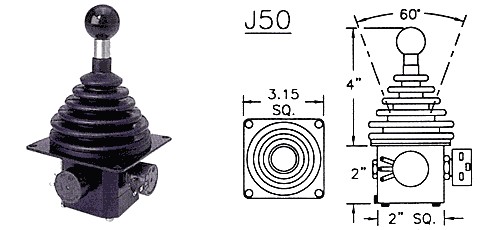
Two axis joystick 4″ handle height 60° deflection angle ( ± 30°) Ball knob Spring return to center Circular deflection pattern 10K ohm precision potentiometer Protective rubber boot (IP54 rating above panel) IP65 option available upon special request Panel mounting bracket
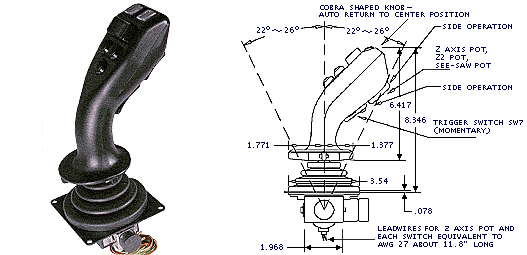
Multi-axis joystick 8.34″ handle height 45° deflection angle ( ± 22.5°) Spring return to center Cobra Head handle Circular deflection pattern 10K ohm precision potentiometers – all axis Three momentary switches (two illuminated, one trigger) Panel mounting bracket Protective rubber boot (IP65 rating above panel)
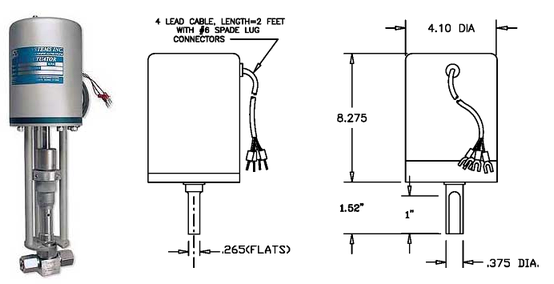
Input: 4 to 20 mA (200 ohms) or 0 to 10VDC (18KΩ) Rotation Speed : 1.5, 3, 5, 10, 20 or 40 RPM Power : 24 VDC (50 Watts min.) Dynamic Braking : Installed Limit Switches : Installed Torque Limiter : Set for Valve requirements. Wt : Approx. 21 in/lbs. max. Seating Limiter : Set […]
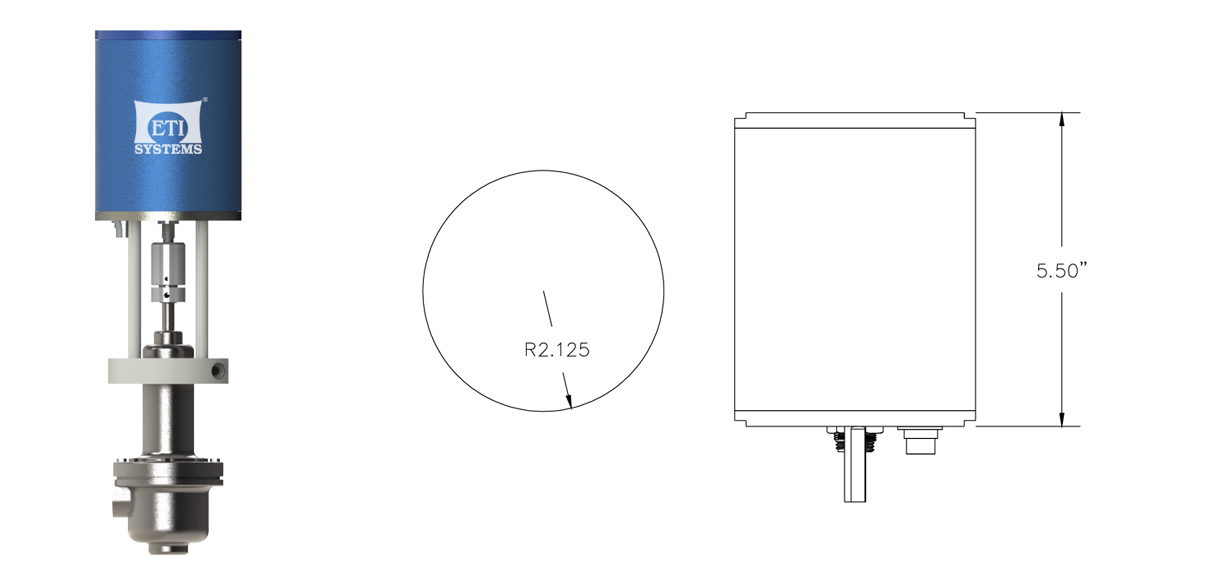