Hydraulic Actuators: Embracing Hydraulic Actuators for Enhanced Performance
Welcome to the world of hydraulic actuators, where power meets precision and performance reaches new heights! In this exciting blog post, we dive into the fascinating realm of hydraulic actuators and explore how they have revolutionized various industries with their unparalleled capabilities. From heavy machinery to aerospace applications, these dynamic devices are embracing innovation like never before, paving the way for enhanced efficiency and superior functionality. So buckle up as we embark on a thrilling journey through the wonders of hydraulic actuators – get ready to be amazed!
Introduction to Hydraulic Actuators
Hydraulic actuators are devices that use hydraulic fluid to generate linear or rotary motion. Hydraulic actuators are often used in industrial and construction applications where large forces are required. However, they can also be used in smaller applications such as automotive brakes and door locks.
Hydraulic actuators typically consist of a cylinder and a piston. The piston is connected to a rod which extends out of the cylinder. When hydraulic fluid is forced into the cylinder, the piston is pushed outwards, causing the rod to move. The amount of force that can be generated by a hydraulic actuator depends on the area of the piston and the pressure of the hydraulic fluid.
Hydraulic actuators have many advantages over other types of actuators. They are very compact, which makes them ideal for use in space-restricted applications. They are also very powerful for their size and can generate high levels of force. In addition, they are relatively simple to maintain and repair.
Disadvantages of hydraulic actuators include the fact that they require a constant supply of hydraulic fluid, which can be expensive to operate. In addition, they can be noisy and may leak if not properly maintained.
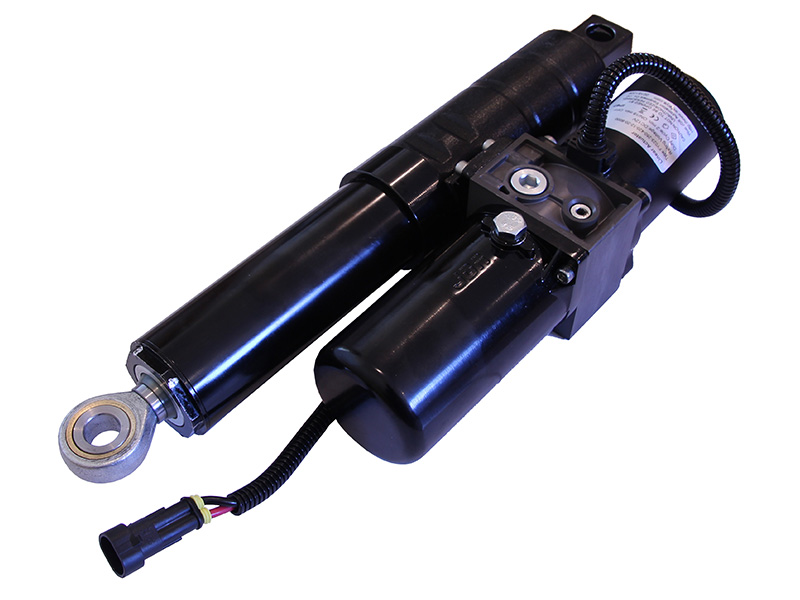
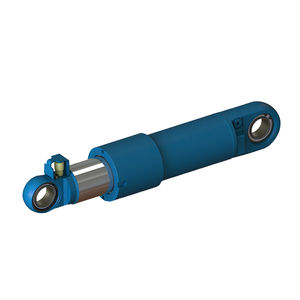
Advantages of Using Hydraulic Actuators
Hydraulic actuators have a number of advantages that make them an attractive option for many applications. Hydraulic actuators are very powerful, meaning they can generate large forces. This high force output makes hydraulic actuators ideal for use in situations where high force is required, such as in construction or manufacturing. Another advantage of hydraulic actuators is their high speed. Hydraulic actuators can move very quickly, which is beneficial in applications where speed is important. Additionally, hydraulic actuators are very durable and have a long lifespan.
Hydraulic actuators also offer excellent control. These actuators can be adjusted to very precise settings, allowing for more accurate control over the motion of the device. Finally, hydraulic actuators are relatively easy to maintain and operate. Many models require minimal maintenance, which can save time and money.
Overall, hydraulic actuators offer a number of attractive advantages that make them an excellent choice for many applications. They are powerful, fast, durable, and easy to maintain. Additionally, they offer excellent control over motion and settings.
Different Types of Hydraulic Actuators
Hydraulic actuators come in a variety of shapes and sizes, each designed for specific applications. The most common types of hydraulic actuators are:
-Piston actuators: These actuators use a piston to generate linear force and motion. They are the most common type of hydraulic actuator and are used in a wide range of applications, from automotive brakes to construction equipment.
-Vane actuators: Vane actuators use a rotating vane to generate linear or rotary force and motion. They are commonly used in hydraulic pumps and motors.
-Cylinder actuators: Cylinder actuators use a piston within a cylinder to generate linear force and motion. They are commonly used in industrial applications, such as presses and lifting equipment.
-Hydrostatic actuators: Hydrostatic actuators use a pressurized fluid to generate linear or rotary force and motion. They are commonly used in systems with variable speed control, such as agricultural and construction equipment.
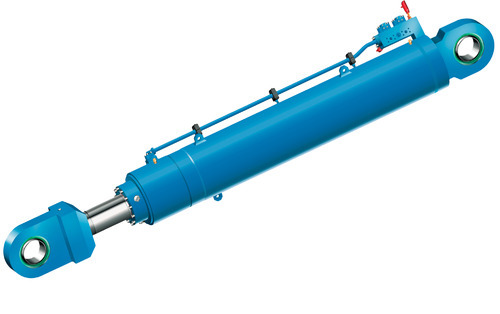
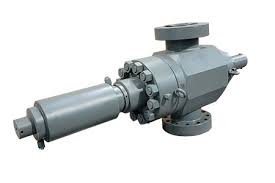
Design Considerations for Hydraulic Actuators
When it comes to choosing the right hydraulic actuator for an application, there are a number of design considerations that need to be taken into account. These include the type of fluid used, the operating pressure, the bore size and stroke length, as well as the mounting arrangements.
The type of fluid used is an important consideration, as different fluids have different properties that can affect performance. For example, water has a lower density than oil, so it can’t provide as much force per unit volume. However, water is also less viscous than oil, so it can flow more easily and is less likely to cause wear on internal components.
The operating pressure is another important consideration, as this will determine the amount of force that can be generated by the actuator. Higher pressures will result in higher forces, but may also lead to increased wear and tear on components.
The bore size and stroke length are also important considerations, as they will determine the overall size and shape of the actuator. Larger bores and longer strokes will result in larger actuators that can generate more force, but they may also be more difficult to mount and operate.
Mounting arrangements need to be considered when selecting a hydraulic actuator. The most common arrangement is a single-acting piston mounted in a cylinder, but other arrangements are possible depending on the application requirements.
How to Choose the Right Hydraulic Actuator?
When it comes to choosing the right hydraulic actuator, there are a few key factors to keep in mind. First and foremost, you need to consider the force or load that will be exerted on the actuator. This will determine the size and type of actuator you need. Secondly, you need to take into account the speed at which the actuator needs to operate. This will help you choose an actuator with the appropriate response time. You need to consider the environment in which the actuator will be used. This includes factors such as temperature and humidity. By taking all of these factors into consideration, you can be sure to choose an actuator that will meet your specific needs and requirements.
It is also important to think about the type of hydraulic actuator you need. There are a variety of types available, each with its own advantages and disadvantages. Some of the most commonly used types are vane, piston, and rotary actuators. Depending on your application, one type may be more suitable than another. It is important to do your research to ensure that you choose the right one for your specific application.
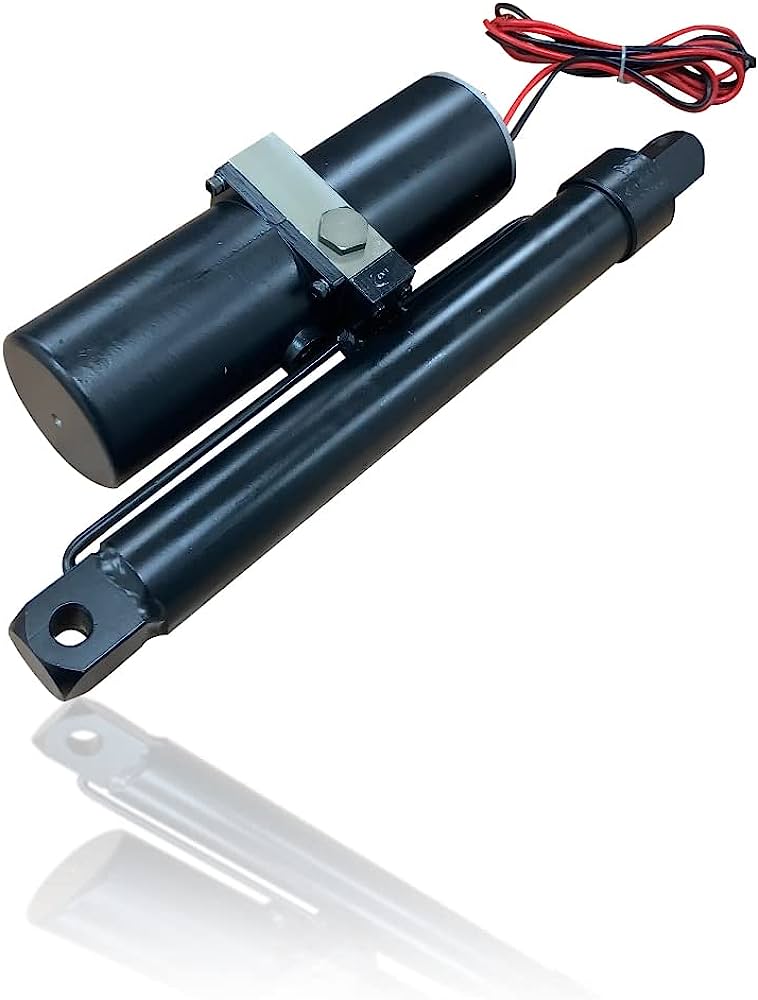
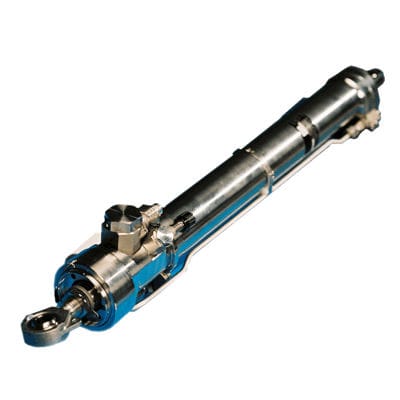
Maintenance Requirements for Hydraulic Actuators
Hydraulic actuators are devices that use hydraulic fluid to generate force in a linear or rotary motion. They are widely used in industrial and mobile applications because of their high power density, precision, and ruggedness. Although they require little maintenance, regular checks are necessary to ensure proper operation.
The most important maintenance requirement for hydraulic actuators is to keep the hydraulic fluid clean and free of contamination. The best way to do this is to use a closed-loop system with a filter. The filter should be checked regularly and replaced as needed. Another way to keep the fluid clean is to flush the system with fresh fluid periodically.
Another important consideration is the condition of the seals. Hydraulic actuators have seals that prevent leakage of fluid between the moving parts. These seals can degrade over time and need to be replaced periodically. It is also important to check for leaks in the system and repair them as soon as possible.
It is important to keep the actuator itself clean and free of debris. This can be done by regularly wiping down the exterior with a damp cloth. If more thorough cleaning is required, disassembly and cleaning of the interior components may be necessary.
Conclusion
Hydraulic actuators are an excellent way to enhance performance and gain a competitive edge. Whether you’re looking for increased power or precision, hydraulic actuators can help achieve your goals without breaking the bank. By learning more about how these devices work and embracing them in your operations, you can ensure that your system performs at its highest level with minimal effort.
Our Products
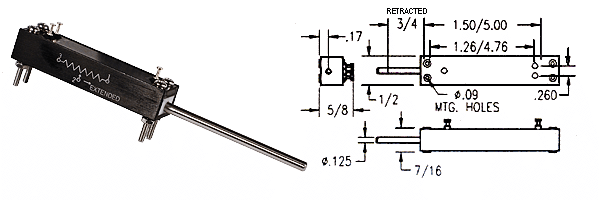
Conductive Plastic Element Black Anodized Aluminum Body, Stainless Steel Shaft, Gold Plated Terminals Recommended for Test and Lab Equipment, Industrial Applications, Medical Equipment (non-life support) Life Expectancy: 20 million strokes Resistance Tolerance: 20% standard (10% Available) Linearity Tolerance: .5% to 1.5% standard (0.3% to 1.0% Available) Power Rating: 0.2 to 1.2 Watt Electrical Stroke: 1″ […]
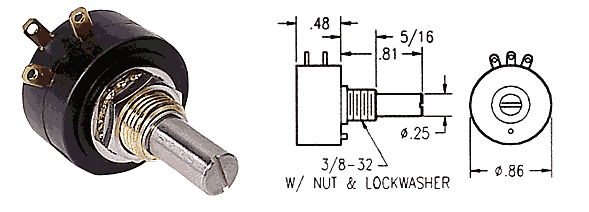
Conductive Plastic Element. Gold Plated Terminals. High Temp. Thermoplastic Housing. Stainless Steel Shaft. Recommended for Medical Equipment (non-life support), Robotics, Industrial, Test and Lab Equipment. Life Expectancy: 10 million turns Resistance Tolerance: ± 10% standard ( ± 10% available) Linearity Tolerance: ± 1.0% standard ( ± 0.5% available) Electrical Angle: 320º ± 5º Mechanical Angle: […]
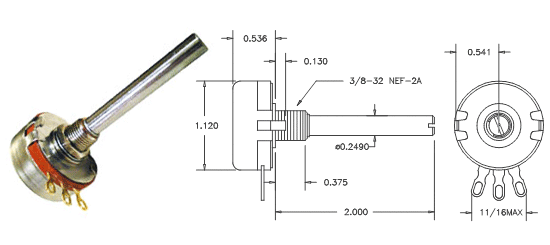
Hot molded carbon element Gold-plated terminals Stainless-steel shaft and housing Quality meeting or exceeding MIL-R-94 – QPL listed Rotational Life: 25,000 Resistance Tolerance: ± 10% or ± 20% Operating Temperature Range: -65°C to +125°C Power rating: 2 watts Insulation Resistance – dry: 10K Meg; wet: 100K Meg Dielectric Strength: 900 VRMS Starting Torque: 1 oz/in […]
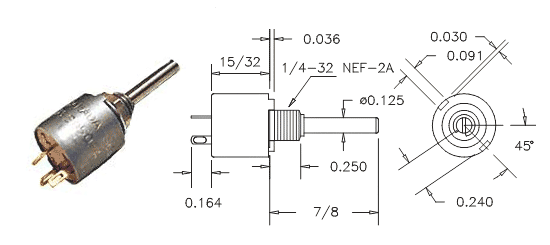
Hot molded carbon element One piece housing and bushing Stainless-steel shaft Quality meeting or exceeding MIL-R-94 – QPL listed Rotational Life: 25,000 Resistance Tolerance: ± 10% or ± 20% Operating Temperature Range: -65°C to +125°C Power rating: 0.5 watts Insulation Resistance – dry: 10K Meg; wet: 100K Meg Dielectric Strength: 750 VRMS Operating Torque: 0.5 […]
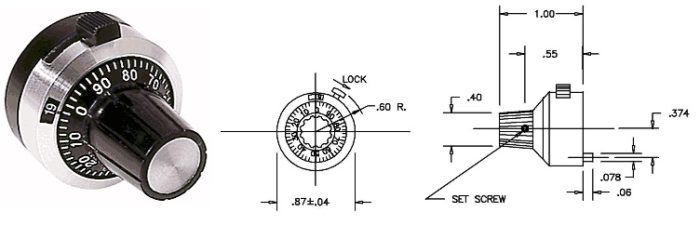
MG22 Concentric Turns Counting Dial Counts up to 20 turns. One Piece Mounting. Aluminum Housing. Black Nylon Knob. Numbers are White on Black Background. Over the Center Lock Available. Diameter – 7/8″; Extension from Panel – 1.0″ Maximum Panel Thickness – 1/4″ Weight: .2 oz
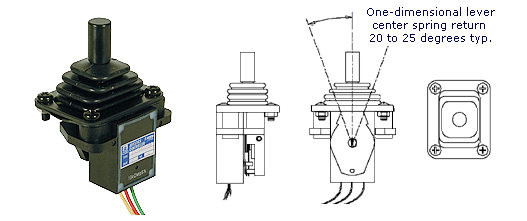
Electrical Specifications: 10K ohm precision potentiometer Single axis joystick Cylindrical knob Linearity (independent): ± 5.0% Lever Electrical Angle: 40° Max. Resolution: Essentially Infinite Mechanical Specifications: ± 20° from center deflection angle Life expectancy: 5 million operations Spring return to center Housing material: High temp. thermoplastic IP65 Rating
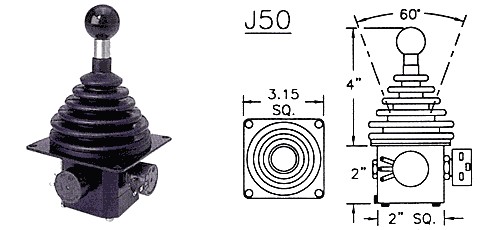
Two axis joystick 4″ handle height 60° deflection angle ( ± 30°) Ball knob Spring return to center Circular deflection pattern 10K ohm precision potentiometer Protective rubber boot (IP54 rating above panel) IP65 option available upon special request Panel mounting bracket
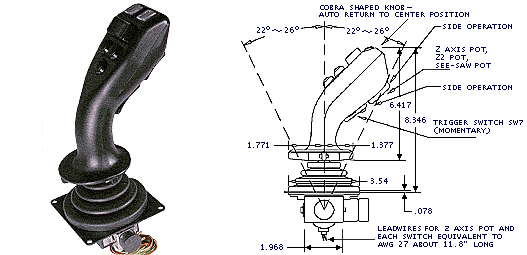
Multi-axis joystick 8.34″ handle height 45° deflection angle ( ± 22.5°) Spring return to center Cobra Head handle Circular deflection pattern 10K ohm precision potentiometers – all axis Three momentary switches (two illuminated, one trigger) Panel mounting bracket Protective rubber boot (IP65 rating above panel)
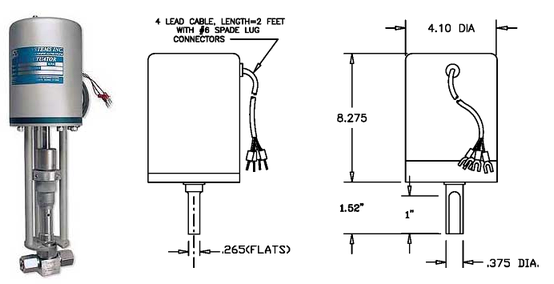
Input: 4 to 20 mA (200 ohms) or 0 to 10VDC (18KΩ) Rotation Speed : 1.5, 3, 5, 10, 20 or 40 RPM Power : 24 VDC (50 Watts min.) Dynamic Braking : Installed Limit Switches : Installed Torque Limiter : Set for Valve requirements. Wt : Approx. 21 in/lbs. max. Seating Limiter : Set […]
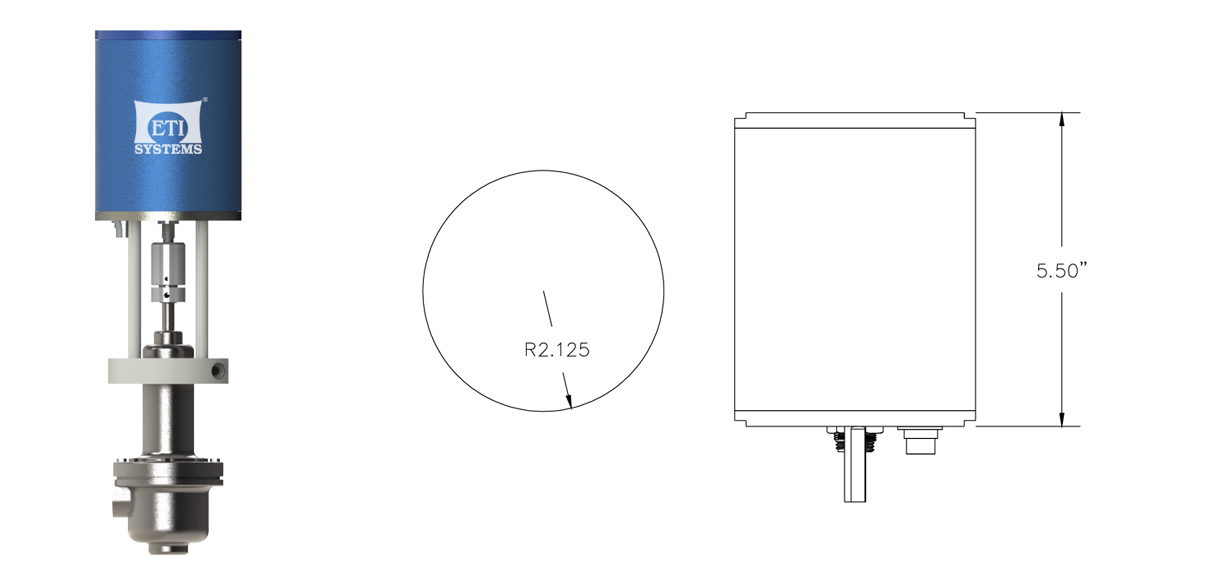