Actuators Unveiled: Powering Progress and Precision in Today's Innovations
Step into a realm where objects awaken, seemingly guided by their own volition. Beneath this captivating spectacle resides the influence of actuators, the uncelebrated champions of contemporary technology. From the subtle vibrations of your smartphone to the orchestrated dance of robotic arms constructing vehicles on factory floors, these adaptable wonders have reshaped our reality in unforeseen ways. Embark with us on a journey into the astonishing domain of actuators – brace yourself for an extraordinary revelation!
What is an Actuator?
An actuator is a device that converts energy into motion. Actuators are used in a wide variety of applications, from automotive engines to computer hard drives. In general, an actuator consists of a power source (such as an electric motor or hydraulic pump), a control system, and a mechanical component (such as a piston or gear).
The term “actuator” is derived from the Latin word “actuarius,” which means “one who sets in motion.” The first recorded use of the word dates back to 1632, when it was used in reference to a device that opened and closed valves. Today, the term is used to describe any device that produces physical movement.
Read More
Most actuators consist of four basic parts: a power source, a control system, a mechanical component, and an output interface. The power source provides the energy needed to produce motion, while the control system regulates the amount of energy supplied to the actuator. The mechanical component converts the energy into motion, and the output interface connects the actuator to its load or application.
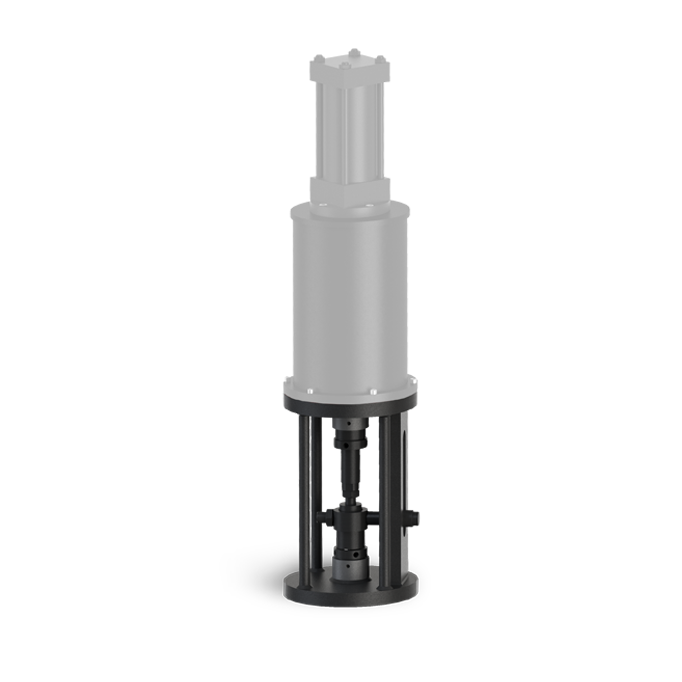
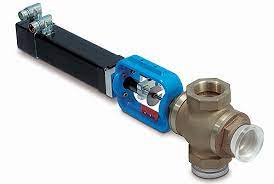
How does an Actuator work?
An actuator is a fascinating device that brings mechanical systems to life. It operates by converting various forms of energy into motion, making it an essential component in a wide range of applications.
At its core, an actuator takes an input signal, often in the form of electrical, hydraulic, or pneumatic energy, and transforms it into a precise movement. This movement can be linear, rotary, or oscillatory, depending on the type of actuator and its intended purpose.
In simpler terms, think of an actuator as the “muscle” behind the mechanics. When you press a button, send an electrical signal, or apply pressure, the actuator responds by generating force or torque, initiating movement in a specific direction. This motion can be as simple as opening a valve or as complex as adjusting the position of a robotic arm.
Read MoreOverall, the versatility and functionality of actuators make them indispensable in modern engineering and automation. They play a vital role in industries ranging from manufacturing and robotics to aerospace and automotive, providing the dynamic motion needed to bring machines and systems to life.
Different types of Actuators
Actuators come in a variety of types, each tailored to specific applications and mechanisms. Here are some common types of actuators:
1. Electric Actuators: These use electric motors to generate movement. They are precise, controllable, and widely used in various applications, from robotics to HVAC systems.
2. Hydraulic Actuators: Hydraulic actuators use pressurized fluids, typically oil, to create force and motion. They are known for their high force output and are used in heavy machinery and industrial systems.
3. Pneumatic Actuators: These use compressed air to create motion. They are often chosen for their simplicity, cost-effectiveness, and quick response times. Pneumatic actuators are used in tasks like opening and closing valves.
4. Linear Actuators: Linear actuators produce motion in a straight line, moving objects along a linear path. They are common in applications where precise linear movement is required, such as in conveyor systems and medical equipment.
Read More
6. Solenoid Actuators: Solenoids are electromagnetic devices that convert electrical energy into linear or rotary motion. They are often used in applications like door locks, valves, and automatic switches.
7. Piezoelectric Actuators: These actuators use the piezoelectric effect to produce motion when subjected to an electric field. They are used in nanotechnology, precision positioning, and fine adjustments.
8. Shape Memory Alloy (SMA) Actuators: SMA actuators change shape in response to changes in temperature. They find applications in areas like aerospace and medical devices.
9. Thermal Actuators: These actuators use thermal expansion to create motion. They are used in devices like thermostats and bimetallic switches.
10. Muscle Wire Actuators: Also known as nitinol actuators, these use a shape memory alloy to generate movement when heated.
The choice of actuator depends on factors such as the required motion type, force, speed, precision, and the environment in which it will be used. Each type has its own advantages and limitations, making it important to select the right one for a specific application.
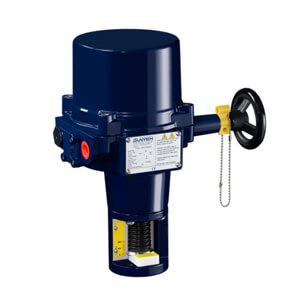
Applications of Actuators in Modern Technology
Actuators play a vital role in many modern technologies, from medical devices to robotics. Here are some of the key ways actuators are used in today’s world:
- Medical Devices: Actuators are used in a variety of medical devices, from artificial limbs to heart pumps. They provide the necessary force to move these devices, and can be controlled remotely to ensure precise movements.
- Robotics: Many industrial and commercial robots use actuators to move their various parts. This allows them to perform tasks such as welding, painting, and fabricating with high levels of accuracy and repeatability.
- Automotive: In recent years, actuators have been increasingly used in automotive applications. They are used in everything from active suspension systems to brake-by-wire systems. This trend is expected to continue as vehicles become more autonomous.
- Aerospace: Actuators are also widely used in the aerospace industry, where they power aircraft control surfaces such as flaps and rudders. They are also used in rockets and satellites for attitude control.
- Consumer Electronics: Actuators are found in a number of consumer electronics products, including digital cameras and camcorders (for optical image stabilization), gaming controllers (for vibration feedback), and mobile phones (for haptic feedback).
Actuator in control system
Read MoreActuators are the “doers” in a control loop. They receive output signals from the controller, which contain instructions on how the system should respond to achieve a desired outcome. Depending on the type of control system and the application, actuators can perform a wide range of actions, such as opening or closing valves, adjusting positions, generating force, or altering parameters like temperature and pressure.
Here’s how an actuator works within a control system:
Controller Output: The control system’s controller processes input signals and calculates the required response. It generates control signals or setpoints that define the desired action.
Actuator Input: The control signals from the controller serve as input to the actuator. The actuator interprets these signals and converts them into physical actions or adjustments.
Physical Action: Based on the received control signals, the actuator initiates the necessary physical action. For example, if the control system is managing the temperature in a room, the actuator might adjust the position of a heating valve to regulate the heat output.
Feedback Loop: Many control systems include a feedback loop where sensors monitor the actual system state and provide feedback to the controller. The controller adjusts its output signals based on the feedback received, ensuring the desired outcome is achieved.
System Response: The actuator’s movement or adjustment influences the system’s behavior, bringing it closer to the desired state as instructed by the controller.
Continuous Control: The control loop operates continuously, with the actuator responding to updated control signals and feedback from sensors. This allows the system to maintain the desired state or follow a specified trajectory.
Overall, the actuator’s role is to bridge the gap between the control signals generated by the controller and the physical actions required to achieve the desired control system outcome. It is a key element in ensuring accurate, efficient, and responsive control of various processes and systems.
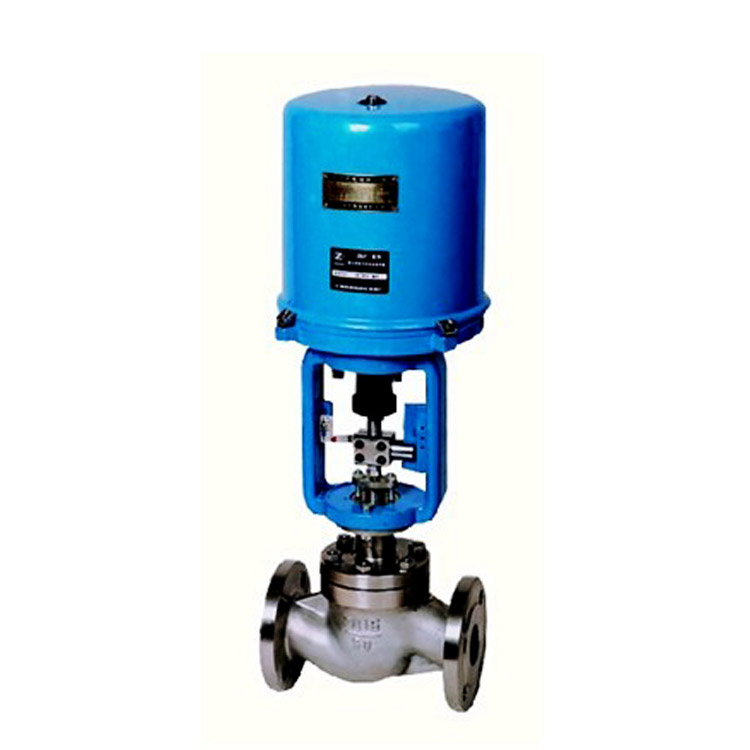
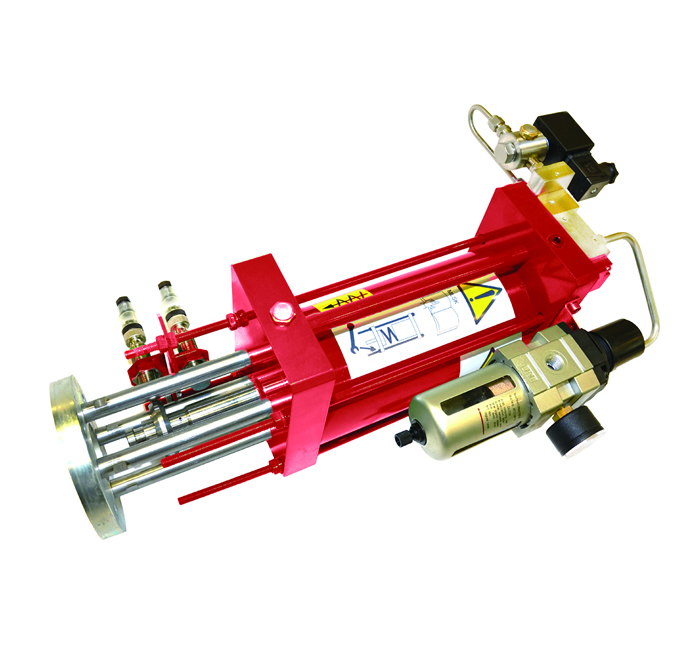
Benefits of Using Actuators in Technology
Actuators are devices that convert energy into motion. They are an essential component of many types of machinery, including automobiles, aircraft, and manufacturing equipment. In recent years, actuators have become increasingly popular in consumer electronics, as they offer a compact and efficient way to generate motion.
There are many benefits to using actuators in technology. For one, actuators can be used to create very small and precise movements. This is ideal for delicate tasks such as manipulating microchips or assembling small electronic components. Additionally, actuators can generate a wide range of motions, from simple linear movements to more complex rotary or vibrating motions. This makes them suitable for a variety of applications.
Another benefit of using actuators is that they can be controlled very precisely. This is thanks to the use of feedback mechanisms, which allow the device to adjust its output in response to changes in inputs. This makes actuators ideal for use in automated systems where consistent and accurate operation is essential.
Actuators are very reliable and require little maintenance. Once installed, they will typically operate for many years without requiring any attention. This makes them an attractive option for use in critical applications where downtime would be costly or dangerous.
Advanced Techniques Used for Controlling and Monitoring Actuators
There are many advanced techniques used for controlling and monitoring actuators. One such technique is known as feedback control. Feedback control is a method of regulating a system by using feedback from the system itself. This feedback can be in the form of a signal that represents the system’s output, or it can be in the form of an error signal that represents the difference between the desired output and the actual output.
Another advanced technique used for controlling actuators is known as feed-forward control. Feed-forward control is a method of regulating a system by using information about the system’s inputs to predict its outputs. This information can be in the form of a mathematical model of the system, or it can be in the form of past data from similar systems.
yet another technique is known as PID control which is Proportional–Integral–Derivative controller (PID controller). A PID controller continuously calculates an error value e(t) as the difference between a desired setpoint and a measured process variable and applies correction based on proportional, integral, and derivative terms (denoted P, I, and D respectively).
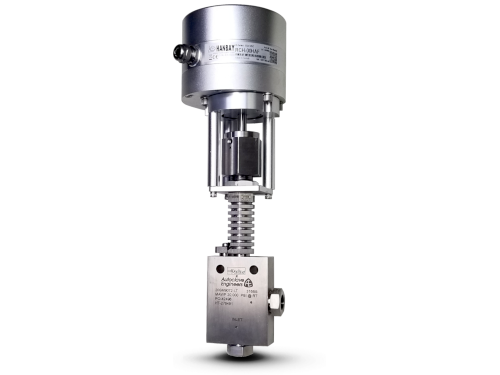
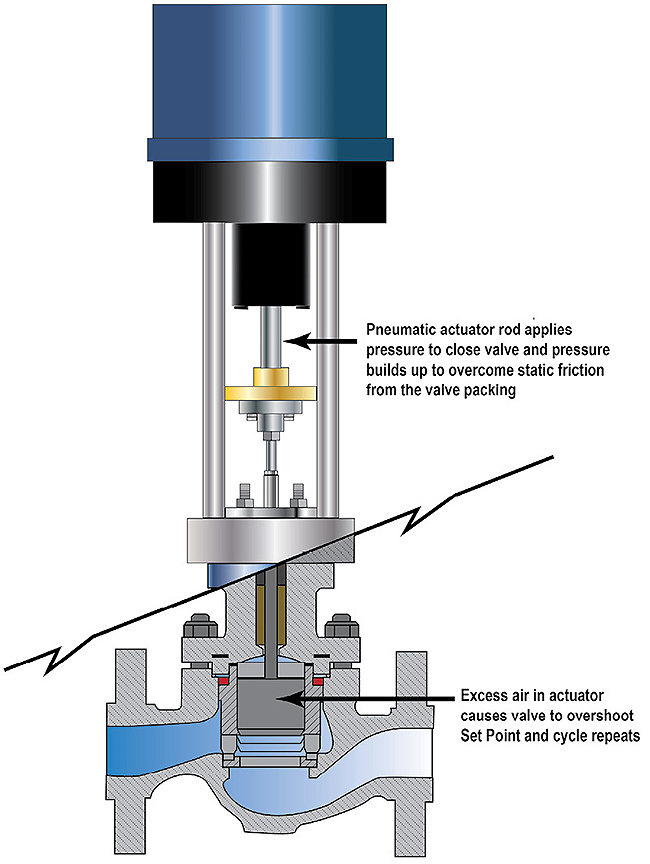
Challenges of Using Actuators in Technology
Actuators are electromechanical devices that convert energy into motion. While they are essential components in a wide range of technologies, from automotive engines to computer hard drives, actuators can pose challenges in terms of design and implementation.
One of the main challenges of using actuators is ensuring that they are able to withstand the high temperatures and pressures that are often present in industrial and commercial applications. Additionally, actuators must be able to operate reliably in dusty or wet environments.
Another challenge is designing actuators that can generate the precise levels of force and movement required for specific applications. For example, some actuators may need to generate very high levels of force, while others may only need to produce relatively small amounts of movement.
It is often necessary to integrate actuators into existing systems and designs. This can be challenging due to the need to maintain compatibility with other components and interfaces.
Conclusion
In conclusion, actuators are an essential component of modern technology and their versatility makes them invaluable in many different applications. From robotics to medical devices to manufacturing systems, the use of actuators is widespread and growing. With advances in technology, more efficient and precise control over motion can be achieved through the use of various types of actuators. As we continue to explore new ways to utilize this versatile piece of equipment, the possibilities for innovation only expand further.
Our Products
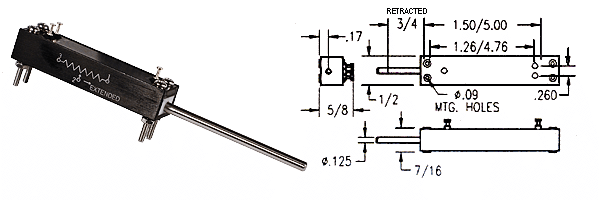
Conductive Plastic Element Black Anodized Aluminum Body, Stainless Steel Shaft, Gold Plated Terminals Recommended for Test and Lab Equipment, Industrial Applications, Medical Equipment (non-life support) Life Expectancy: 20 million strokes Resistance Tolerance: 20% standard (10% Available) Linearity Tolerance: .5% to 1.5% standard (0.3% to 1.0% Available) Power Rating: 0.2 to 1.2 Watt Electrical Stroke: 1″ […]
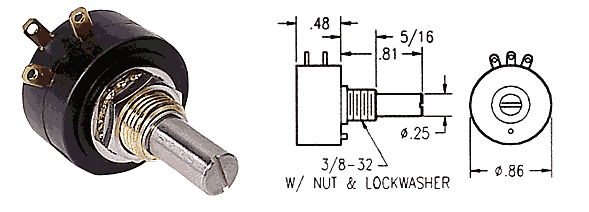
Conductive Plastic Element. Gold Plated Terminals. High Temp. Thermoplastic Housing. Stainless Steel Shaft. Recommended for Medical Equipment (non-life support), Robotics, Industrial, Test and Lab Equipment. Life Expectancy: 10 million turns Resistance Tolerance: ± 10% standard ( ± 10% available) Linearity Tolerance: ± 1.0% standard ( ± 0.5% available) Electrical Angle: 320º ± 5º Mechanical Angle: […]
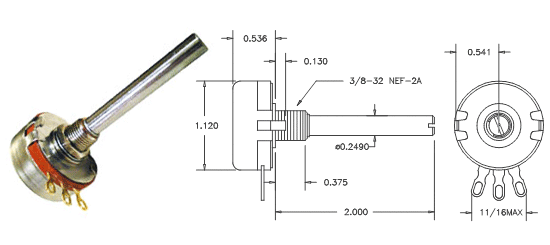
Hot molded carbon element Gold-plated terminals Stainless-steel shaft and housing Quality meeting or exceeding MIL-R-94 – QPL listed Rotational Life: 25,000 Resistance Tolerance: ± 10% or ± 20% Operating Temperature Range: -65°C to +125°C Power rating: 2 watts Insulation Resistance – dry: 10K Meg; wet: 100K Meg Dielectric Strength: 900 VRMS Starting Torque: 1 oz/in […]
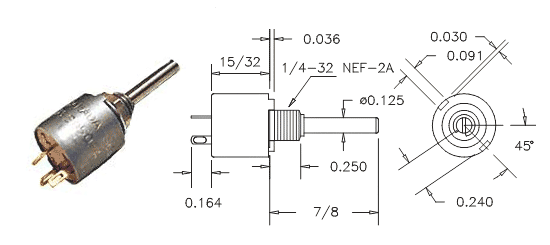
Hot molded carbon element One piece housing and bushing Stainless-steel shaft Quality meeting or exceeding MIL-R-94 – QPL listed Rotational Life: 25,000 Resistance Tolerance: ± 10% or ± 20% Operating Temperature Range: -65°C to +125°C Power rating: 0.5 watts Insulation Resistance – dry: 10K Meg; wet: 100K Meg Dielectric Strength: 750 VRMS Operating Torque: 0.5 […]
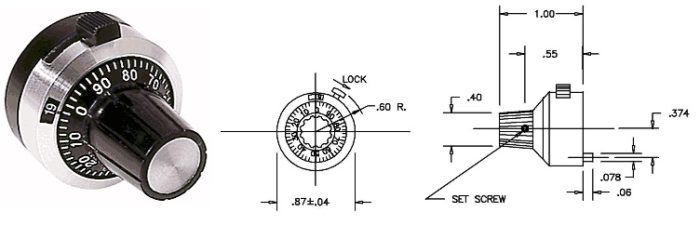
MG22 Concentric Turns Counting Dial Counts up to 20 turns. One Piece Mounting. Aluminum Housing. Black Nylon Knob. Numbers are White on Black Background. Over the Center Lock Available. Diameter – 7/8″; Extension from Panel – 1.0″ Maximum Panel Thickness – 1/4″ Weight: .2 oz
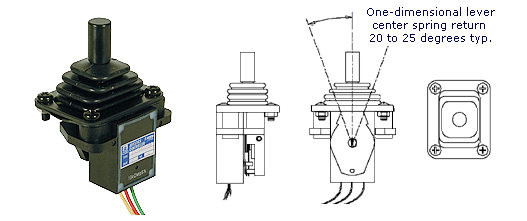
Electrical Specifications: 10K ohm precision potentiometer Single axis joystick Cylindrical knob Linearity (independent): ± 5.0% Lever Electrical Angle: 40° Max. Resolution: Essentially Infinite Mechanical Specifications: ± 20° from center deflection angle Life expectancy: 5 million operations Spring return to center Housing material: High temp. thermoplastic IP65 Rating
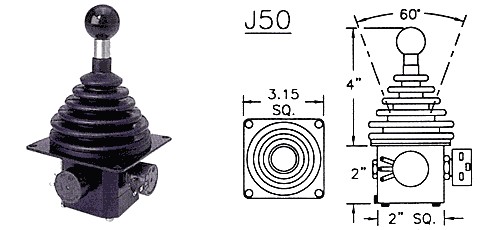
Two axis joystick 4″ handle height 60° deflection angle ( ± 30°) Ball knob Spring return to center Circular deflection pattern 10K ohm precision potentiometer Protective rubber boot (IP54 rating above panel) IP65 option available upon special request Panel mounting bracket
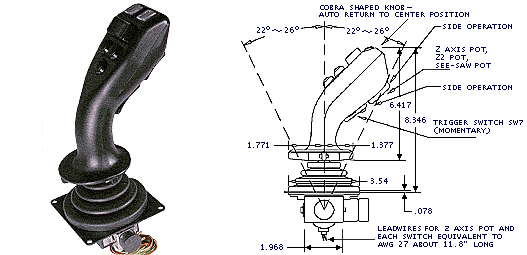
Multi-axis joystick 8.34″ handle height 45° deflection angle ( ± 22.5°) Spring return to center Cobra Head handle Circular deflection pattern 10K ohm precision potentiometers – all axis Three momentary switches (two illuminated, one trigger) Panel mounting bracket Protective rubber boot (IP65 rating above panel)
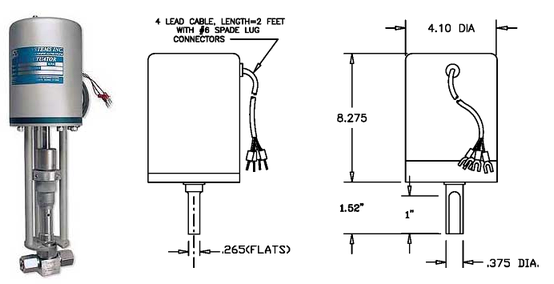
Input: 4 to 20 mA (200 ohms) or 0 to 10VDC (18KΩ) Rotation Speed : 1.5, 3, 5, 10, 20 or 40 RPM Power : 24 VDC (50 Watts min.) Dynamic Braking : Installed Limit Switches : Installed Torque Limiter : Set for Valve requirements. Wt : Approx. 21 in/lbs. max. Seating Limiter : Set […]
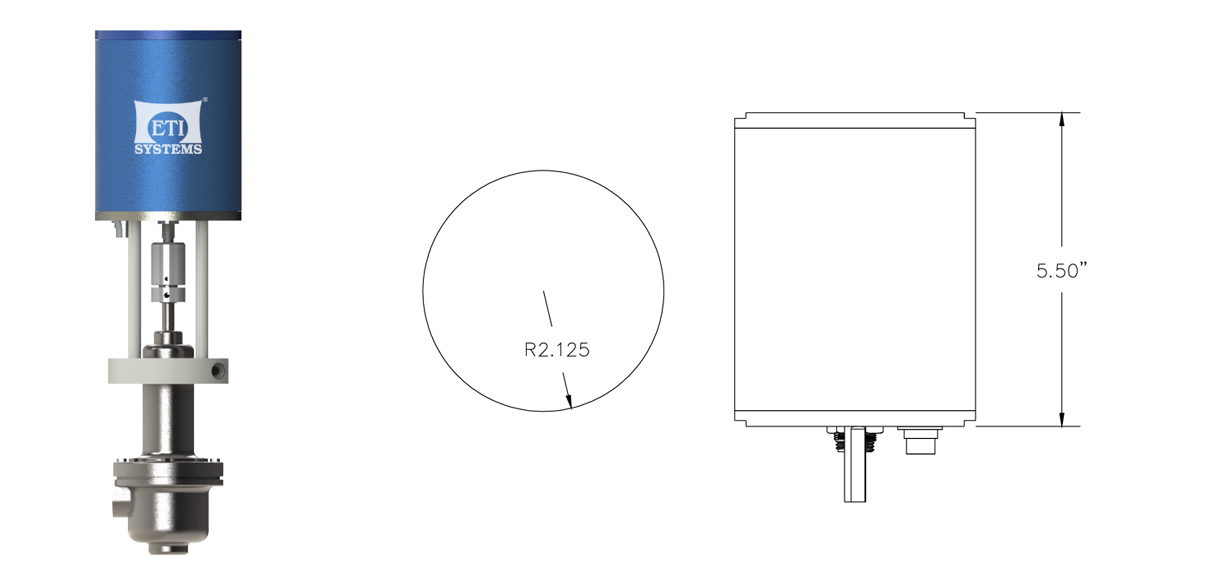